Mujin has automated the parts delivery and finished product retrieval processes using AGVs in the assembly line for semiconductor cleaning equipment at the new building of SCREEN Semiconductor Solutions Co., Ltd. in Hikone, Shiga Prefecture. This automation aims to achieve scalable logistics efficiency with a flexible location management system for parts delivery.
The cell production method has been adopted in this process to flexibly respond to fluctuations in demand for semiconductor cleaning equipment. By integrating the assembly and picking support system with AGVs, Mujin has supported the development of SCREEN’s unique production management system, which includes progress tracking of operations. This integration has reduced the manpower previously required for parts delivery, eliminated errors in parts delivery and picking, and contributed to the construction of a flexible assembly process capable of adapting to changes by utilizing non-fixed equipment like AGVs.
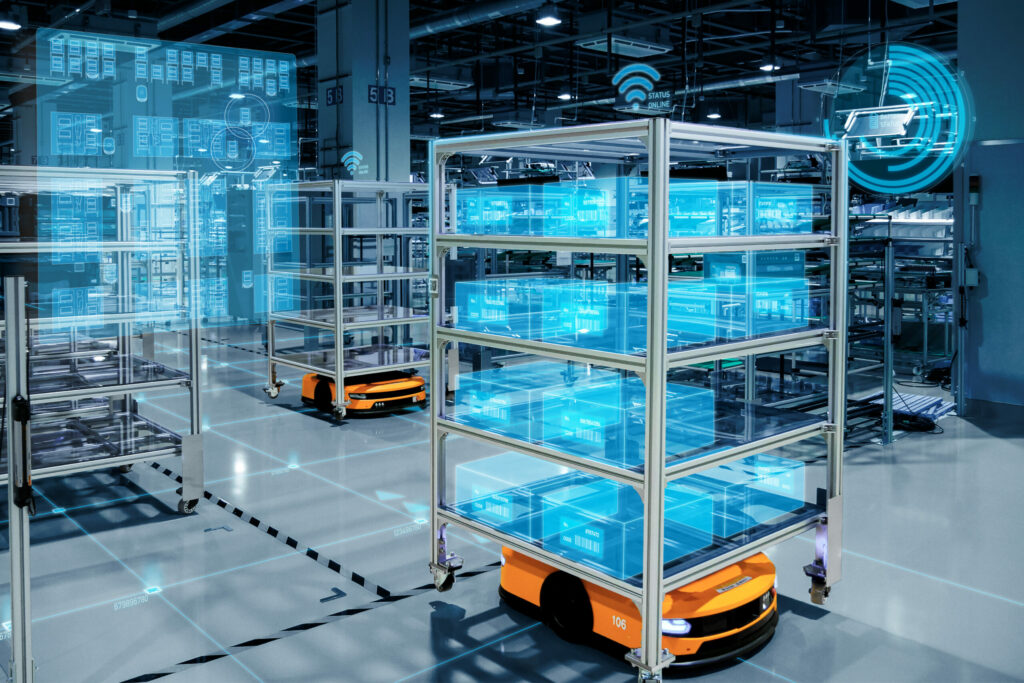
Rapid Implementation
Initially, SCREEN considered adopting AGVs for internal logistics automation based on a new concept that revamped traditional methods such as ceiling conveyance. A key requirement for advancing the project quickly was achieving a short delivery time.
To meet this need, Mujin provided a product and parts inventory supply system capable of responding to the growing demand for internal logistics automation. Our experienced team offered precise specifications to realize the customer’s vision. With the cooperation of SCREEN, we enabled a faster-than-average implementation period from contract signing to system launch.
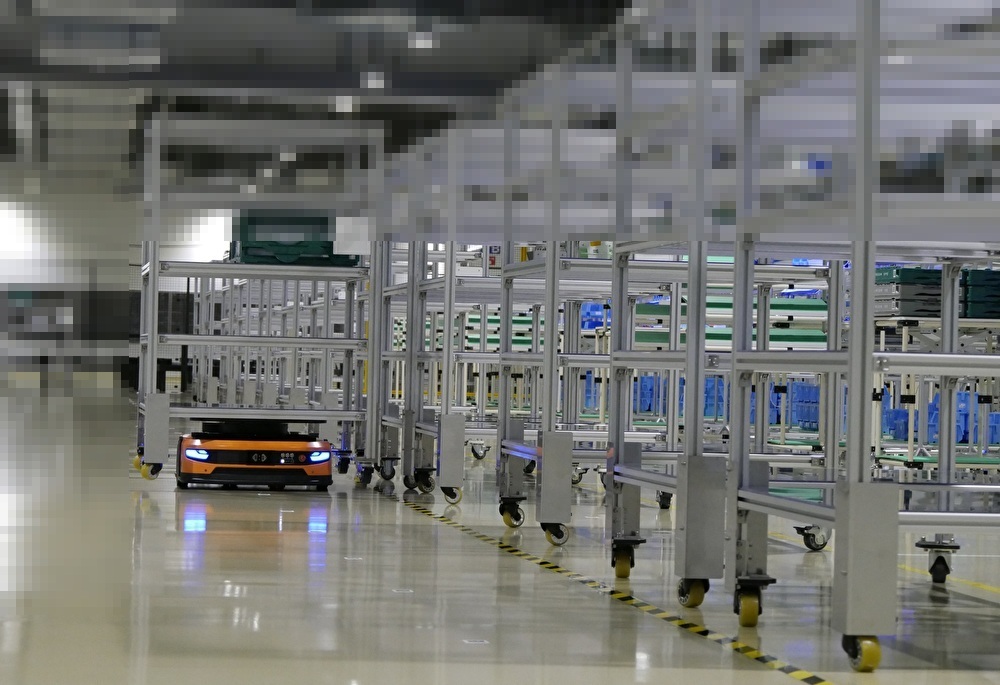
Reliable AGV Support System by Mujin
Mujin’s unique AGV support system offers consistent service from specification determination to post-operation maintenance, leveraging the expertise of a specialist team with extensive on-site experience. This system, capable of meeting the high requirements of manufacturing environments, was developed over several years, centered around our Nagoya office. Today, it has earned high praise from many customers for ensuring reliable AGV usage even after implementation.
QR Grid AGV
Among various types of automated guided vehicles (AGVs) such as magnetic tape and SLAM systems, Mujin offers QR Grid AGVs that are particularly practical for manufacturing and logistics environments. The three key features of QR Grid AGVs are:
1. Group Control for Scale ranging from Several to Hundreds of Units
By automatically controlling collision and congestion avoidance through software, QR Grid AGVs maximize their transport capacity even in environments where multiple AGVs are in operation, ranging from a few units to several hundred.
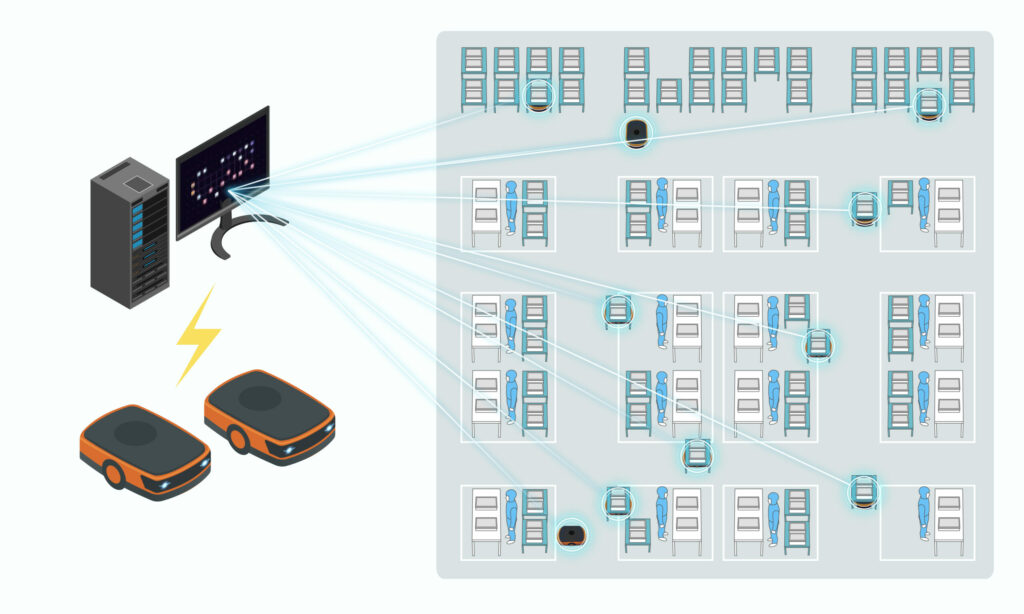
2. Minimization of Travel Area
QR Grid AGVs enable the promotion of automated transportation with minimal space requirements even in limited layouts, achieved through travel that maintains the orientation of the cargo or utilizes 90-degree rotations.
3. Flexible Layout Changes
With QR code placement on the floor and map registration, QR Grid AGVs facilitate easy layout changes, allowing for flexibility in adapting to different configurations.
Mujin has been at the forefront of automation, leveraging intelligent robots and AGVs to automate various processes. In recent years, we have expanded our business from partial optimization to overall optimization by offering next-generation total engineering services for intelligent automation in next-generation factories and warehouses, built on our proprietary automation integration platform. Our next-generation total engineering services cover everything from automation concept planning to equipment design, integration, and remote support, allowing us to support our customers’ supply chain transformation initiatives from conceptualization and strategy development to execution.