MujinRobot Depalletizer automates unloading for Kyowa Shiko Co., LTD., achieving a high capacity of 1,000 cases per hour through its unique robot intelligence software.
Using its intelligent robot system, Mujin has successfully automated the unloading of shipping cases at Kyowa Shiko’s Logistics Center No. 2 with two MujinRobot Depalletizers. With its masterless multi-pick function, the MujinRobot Depalletizer can maintain a high capacity of unloading without requiring case information registration, even when introducing new product types. This has resulted in a 70% increase in shipping capacity and the establishment of a stable shipping system.
Multi-pick and Masterless for Unparalleled Performance
The MujinRobot Depalletizer delivers outstanding performance through its multi-pick and masterless capabilities. By leveraging the MujinVision3D technology as its “eyes” to accurately identify shipping cases, and the MujinController as its “brain” to calculate the robot’s movements, the MujinRobot Depalletizer achieves optimal performance. With the unique “Robot Intelligence Software” integrated into the MujinController, the robot is able to execute optimized movements autonomously, providing unparalleled performance.
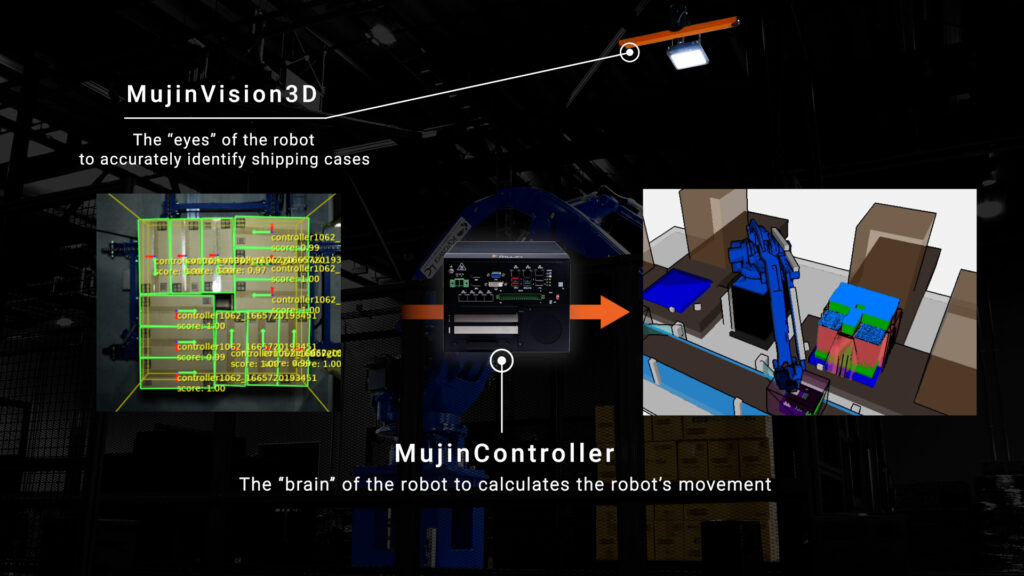
The standout feature of the MujinRobot Depalletizer installed in this center is its masterless implementation of the advanced intelligent software that enables the multi-pick function. This functionality allows the robot to identify the shape and layout of the cases and, whenever feasible, unload multiple cases simultaneously, maximizing its transport capacity. Through its masterless operation, the robot can automatically recognize the shape and arrangement of cases, including new varieties added, and independently calculate and execute the optimal unloading method, including the possibility of multiple picks. The masterless implementation of the multi-pick feature has made it possible for the robot to handle mixed loads, achieving an overwhelmingly high capacity without the need for prior case information registration.
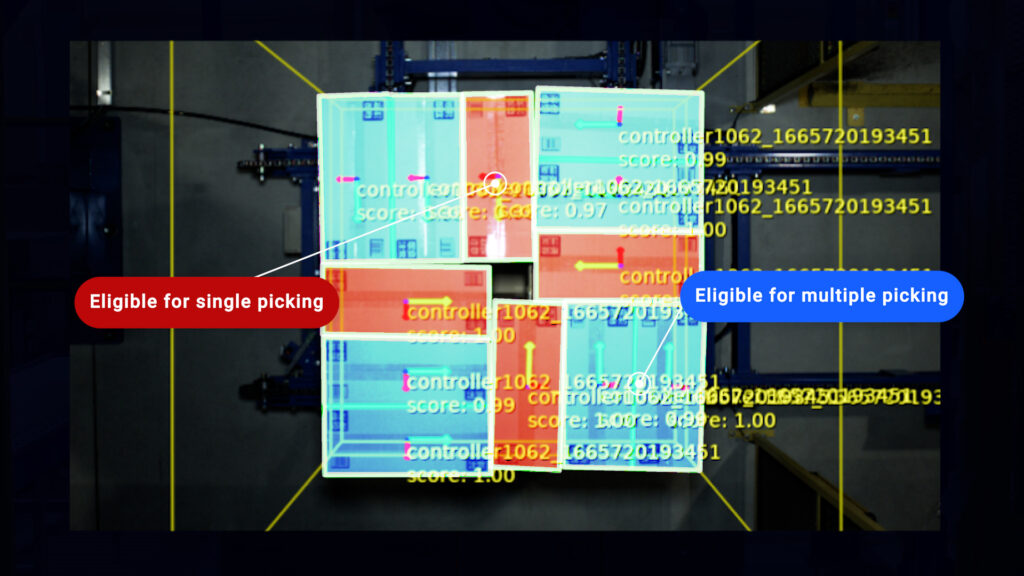
Typically, industrial robots operate on pre-programmed movements (teaching) that require detailed logic to achieve high performance. Additionally, any changes in the robot’s surroundings necessitate reprogramming the appropriate movements.
For instance, to implement a multi-pick function, the cases to be handled must be registered as master cases beforehand, and the robot motion must be programmed with the appropriate multi-pick settings for each case. However, this approach is impractical in the logistics field, where the variety of cases and rapid changes in the environment make it challenging to register cases and reprogram the robot’s motions every time.
Mujin’s “Robot Intelligence Software” addresses these challenges by recognizing objects and the robot’s surroundings in real-time and autonomously generating optimized robot motions, even for a new case without prior information, while considering the surrounding environment. This allows the robot to execute complex functions such as multi-pick without a master, maximizing the robot’s capabilities.
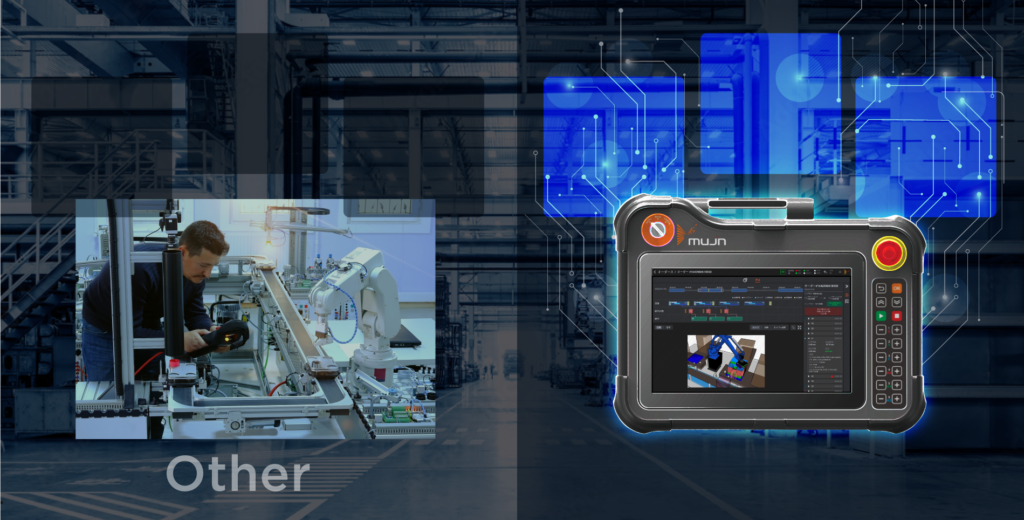
Reduced overtime hours and simplified work planning
Kyowa Shiko is a company that excels not only in product development but also in strengthening its logistics system to support its thriving business. However, like many companies, it struggles to secure stable workers and faces the issue of overtime work during busy seasons. Therefore, the company opted to implement the MujinRobot Depalletizer to address these challenges.
By introducing two MujinRobot Depalletizers, each capable of unloading more than 1,000 cases per hour, the company has achieved the following outcomes:
- Shipping operations can continue uninterrupted by staffing challenges.
- The stable labor force of the robots allows for highly accurate work plans to be formulated.
- Operational efficiency has improved, allowing work to be completed ahead of schedule.
- Shipping capacity has increased by up to 70%, contributing to the company’s bottom line while reducing overtime hours.
Mujin is committed to supporting its customers’ businesses by providing tailored solutions that reduce workloads and improve operations. The MujinRobot Depalletizer is a prime example of this commitment.
The MujinRobot Depalletizer is an automated solution for unloading both single- and mixed-load cases at logistics sites. It can handle a wide range of target workpieces, including corrugated boxes, large paper and plastic bags, and containers. The system is centrally controlled by the MujinController, which means that even if something should go wrong after installation, we have a support system in place that can respond immediately via remote control.
Mujin will continue to work towards providing customized solutions that meet the specific challenges faced by our customers’ logistics sites, ultimately contributing to the improvement of their business operations.