How hard could it possibly be to get a robot to grip a box and move it from “point A” to “point B”?
The gripper design affects overall robot performance and the final design can literally make or break the production line because the gripper design can affect productivity, profitability, and quality. Designing and building the robot grippers can be an incredibly complex and challenging task with many considerations to be taken into account like the mode for gripping an object, how much force it can provide, the fragility of the workpiece, and ensuring the item will not be damaged during transportation (sometimes need to reduce speed). Feedback from the robot must also be considered to ensure proper trajectory execution as well as maintaining a stable grasp until release. Such work can only be done when you have a talented design team that can create any type of ready-to-work cell based on each customer specification.
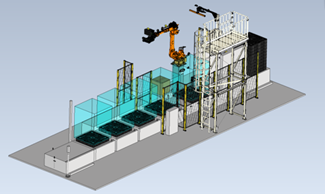
The design team plays an important role at Mujin and is in charge of the robot gripper, facility design, system layout design, equipment selection, and also coming up with new mechatronics systems. Depending on the customer’s specifications, those talents can design new grippers, which require planning, prototype verification, material selection, product design, and operation verification.
Our design engineers use in-house capabilities and innovative approaches to maximize existing options, or design and engineer unique components for ultimate performance in customers’ specific usage and in actual production environments. Before setting up the cell, the team simulates the best position for robot picking, sophisticated task timing, reachability, and the possibility of picking different types of workpieces.
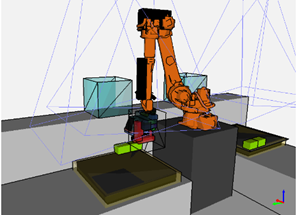
Whether palletizing, depalletizing, picking, or packing, all the necessary components are designed and tested for specific business and technical objectives. Design engineers should consider many key factors, such as workpiece dimensions, weight, and strength, environmental conditions, etc. The important point is that MujinRobot can work with mixed workpieces so the pre-simulation considering the robot’s optimal position or robot cell size should be determined. The robot cell plays an important role in industrial robot installation, so it should be optimized for the space and safety of any operators.
Since the “MujinController” system’s adaptable Machine Intelligence enables robots for almost any task, the design team is in charge of creating and building grippers. The gripper is a device that enables robots to pick up and hold objects. Basically, without a well-developed gripper, it will be difficult to fully utilize the “MujinController” system which may hinder automation.
At first glance, the grippers may appear simple with one or two suction pads connected to the robot arm. But there are many different types of grippers developed by Mujin ranging from small suction cups or fingers to pick small delicate objects to multi-surface “L-shaped” grippers to grab large and heavy objects. Our design team constantly creates new grippers for the customer’s unique application. The choice of the gripper should be determined by the part that the customer intends the robot to pick. Other examples include grippers with tool-changing capabilities, grippers with cameras and sensors for high precision part detection and placement, and grippers that change shape to accommodate the shape of objects. As can be imagined, It is a challenging task, but the Mujin design team always finds a solution.

To date, Mujin has completed many challenging projects. For example, in a recent palletizing project, it was difficult for precise and swift placement of boxes of different sizes properly using a conventional gripper because the customer requested workpieces to be packed into a pallet, a rolling cart, or a cage. In short, using a conventional gripper would not meet the production throughput and workpiece placement stability requirements.
In response, the Mujin design team created a palletizing gripper from scratch in collaboration with the development team and finally tested a prototype. During iREX2022 (iREX2022: Mujin showcased the latest 8 solutions), Mujin showcased a palletizing solution with a custom clamping gripper that lifts the box with suction from the top and also clamps the sides of the boxes to provide increased support and stability. This allows MujinRobot to grasp more securely, and the robot can move faster achieving picking rates of 500 boxes per hour on average. This solution is already serving our customers in real-time.
The design team plays an important role at Mujin, and they need more talent to deal with new cutting-edge projects. This person should be passionate about robotics, and a creative idea generation person who likes to find solutions to new problems. This team values independence, creativity, and quality. Ideally, the candidate has experience in facility design, programming and material handling or robotics, and mechatronics.
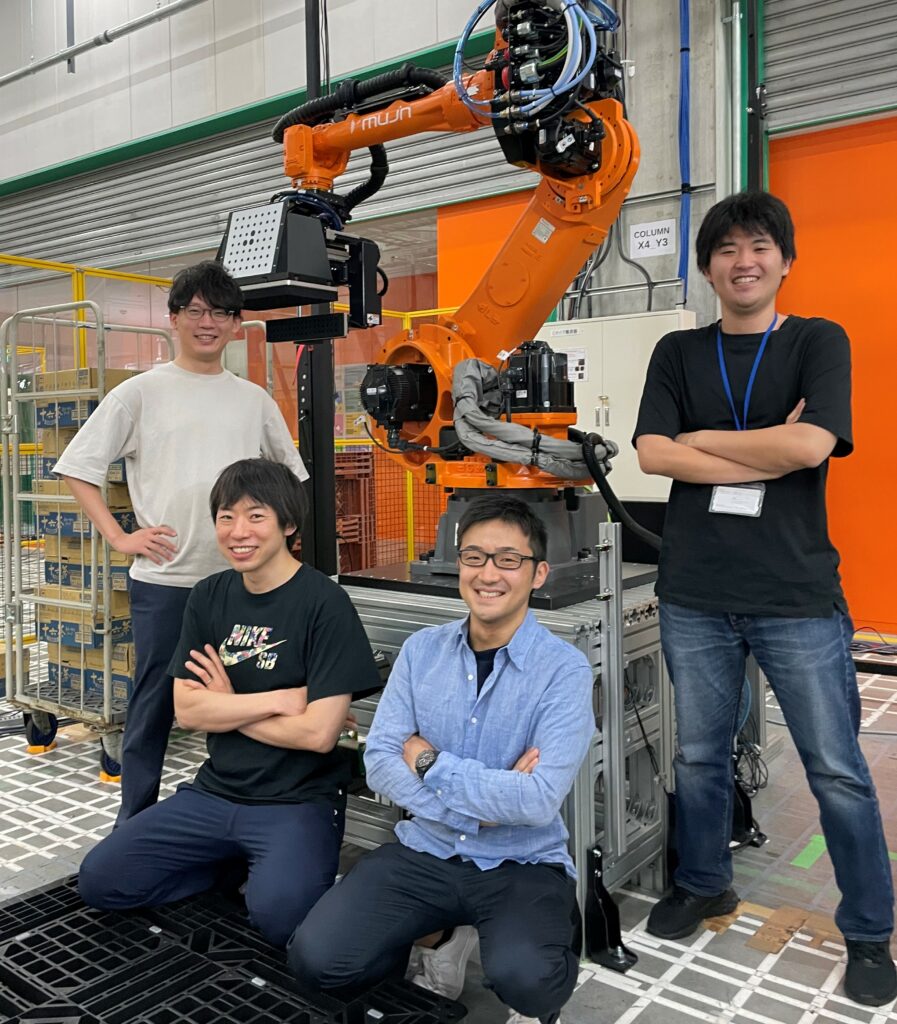
If you think Mujin is the best place for you then just apply :
Mujin CAreer Website