Mujin has been awarded the Robotics Innovation Prize of the Logistics Grand Prizes 2021 for its development of “MujinRobot Palletizer”.
In spite of the heavy workload involved, the automation of mixed case palletizing at logistics centers had been technically difficult in the past. Mujin has realized the automation by developing MujinRobot Palletizer, and was highly evaluated as an excellent initiative to realize “people-friendly logistics” that eliminates high-load work.
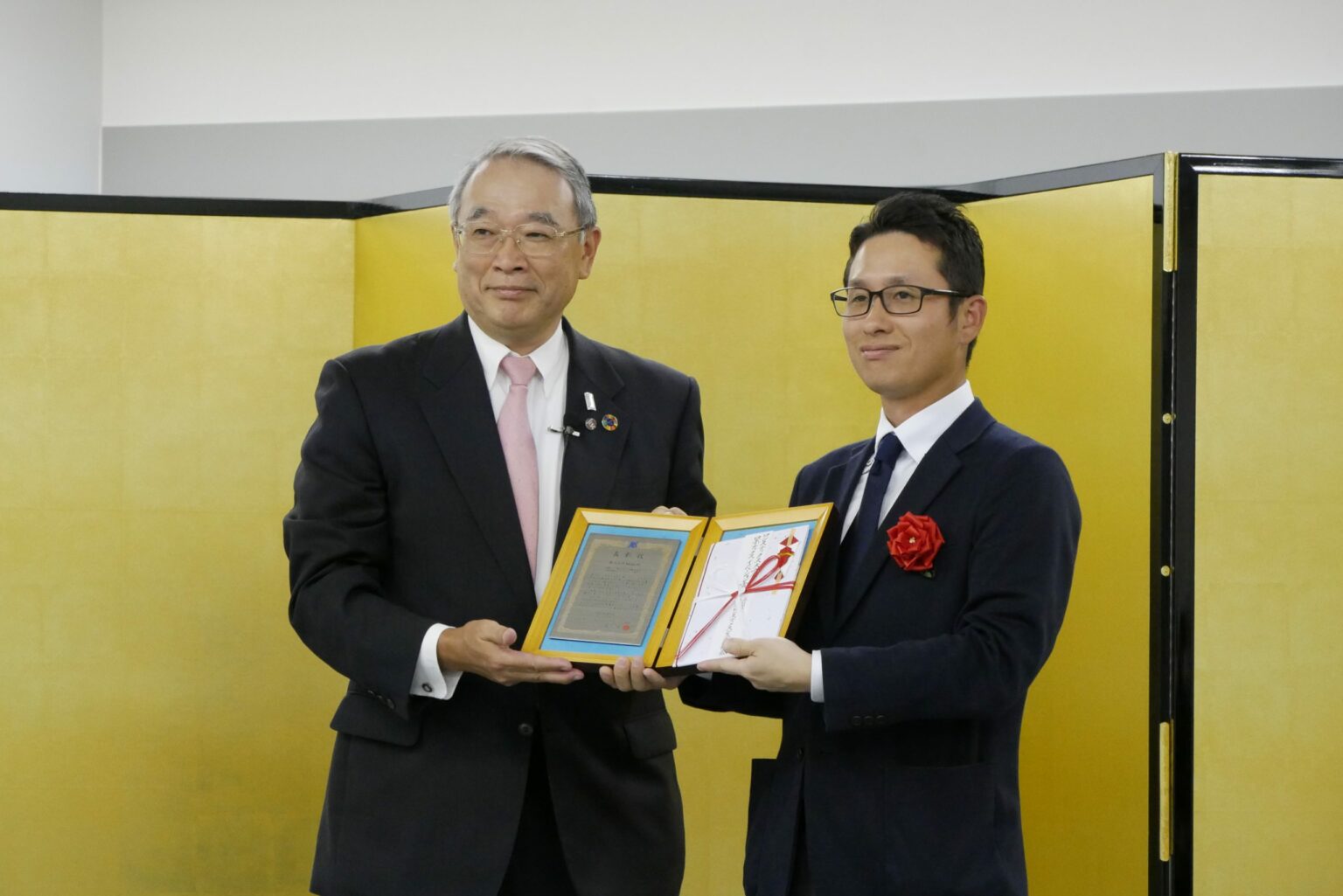
What is the Logistics Grand Prize?
The Logistics Grand Prize, organized by Japan Institute of Logistics Systems, is given for outstanding achievements in the area of logistics promotion by supporting the development of logistics in society and raising the consciousness of those involved in the field of logistics.
The process of palletizing
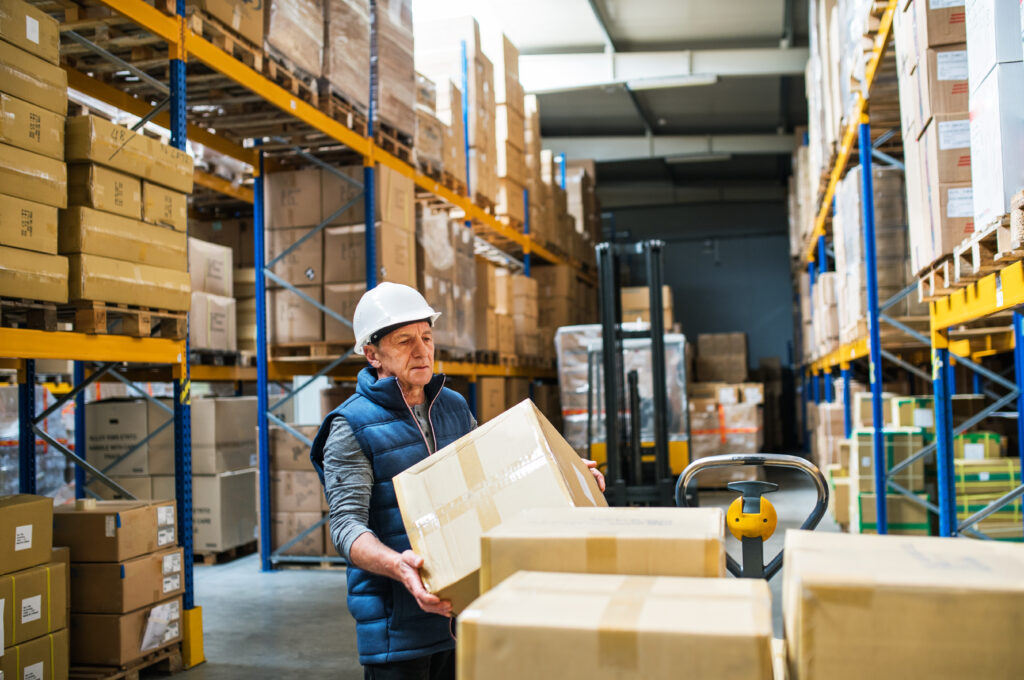
Palletizing is the process of loading cases. This work is mainly done in the shipping process in the warehouse.
<An example of the flow>
① Recieve a picking list with what and how many cases to be shipped to each destination.
② Go find the cases to ship.
③ Load them on loading units such as pallets, cage carts, and cart racks.
④ Take the loading units to the truck for shipment.
Knowing what to put first and how to put them in order is something that can be learned through experience, not something that an inexperienced person can do on the spot. This is a particularly difficult process to secure staff for, because it requires a lot of hard work and experience.
Difficulties in automating palletization
Although there is a high demand for automation of advanced palletizing operations, it has been difficult to achieve a practical level of automation. This is because the level of technical difficulty was extremely high, as every aspect had to be taken into account.
① Optimal packing for the shipper and destination
In the palletizing process, a skilled person in charge usually decides the best palletizing method each time, taking into consideration the following factors.
・ Balance packings so that they don’t collapse
・ Place heavy items underneath to avoid crushing
・ Pack efficiently to minimize the transportation expenses
・ Put items in the same category close together for the efficiency of displaying the products at the shipping destination
② Range of motion of the robot
When the process is automated by a robot, its specific motion limitations must be also considered. The following must be ensured for all trajectories in which the robot moves.
・ Avoid interference of the robot body with loading units.
・ Avoid interference of the robot body with case items
・ Avoid singularities (robot’s postures that are structurally uncontrollable for the robot and cause it to stop)
Therefore, it is necessary to consider not only how to palletize efficiently, but also the limitation of the robot.
③ Ensuring speed and quality
Even if ① and ② are taken into consideration, robots cannot be put to practical use if their processing capacity is low or if they stop at every opportunity. It is necessary to guarantee speed and stability.
The development of MujinRobot Palletizer
Mujin has developed the MujinRobot palletizer to automate this process by overcoming the difficult challenges described above through research and experience gained through the intelligent robot solutions we have provided.
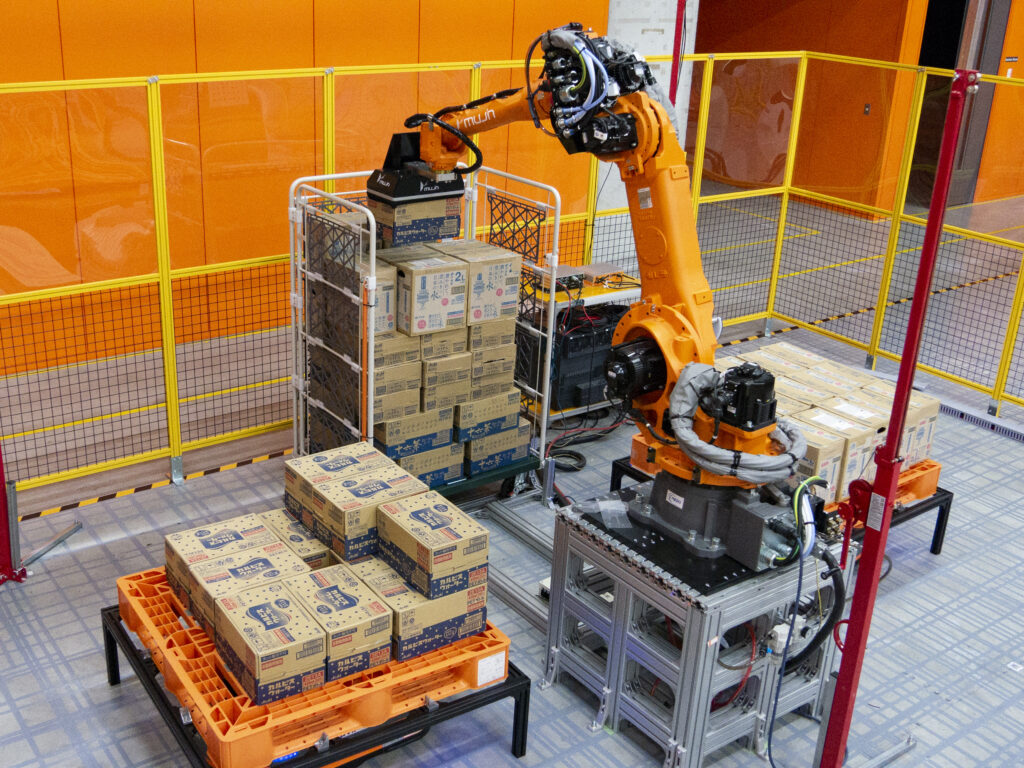
Various functions have been realized to ensure operation at a practical level and avoid unforeseen situations, and are currently in actual use at many sites.
Judge’s Comment
As the working population in Japan continues to decline, the logistics industry is facing a serious shortage of manpower. In addition, there is a need to create a working environment where people can work more easily, and there is a need to free people from heavy work in the warehouse. However, automation has not yet been achieved for operations such as shipping to retail stores, where multiple products with different dimensions, etc., are stacked in a cart rack for shipment.
Under these circumstances, Mujin has developed a robot that can palletize cases of different sizes and weights in a cart ruck, etc., taking into account the rules such as placing heavy items underneath to avoid crushing the load and to prevent it from collapsing, as well as the display efficiency of the destination and the loading efficiency of the truck. In addition to being able to handle multiple loading units such as pallets and cages with a single robot, the robot can detect the distortion of the fixtures and correct the robot’s movement, thus achieving versatility and availability.
This initiative was recognized as an outstanding effort to realize “people-friendly logistics” by eliminating high-load work for people.
(Cited and translated from Japan Institute of Logistics Systems website)
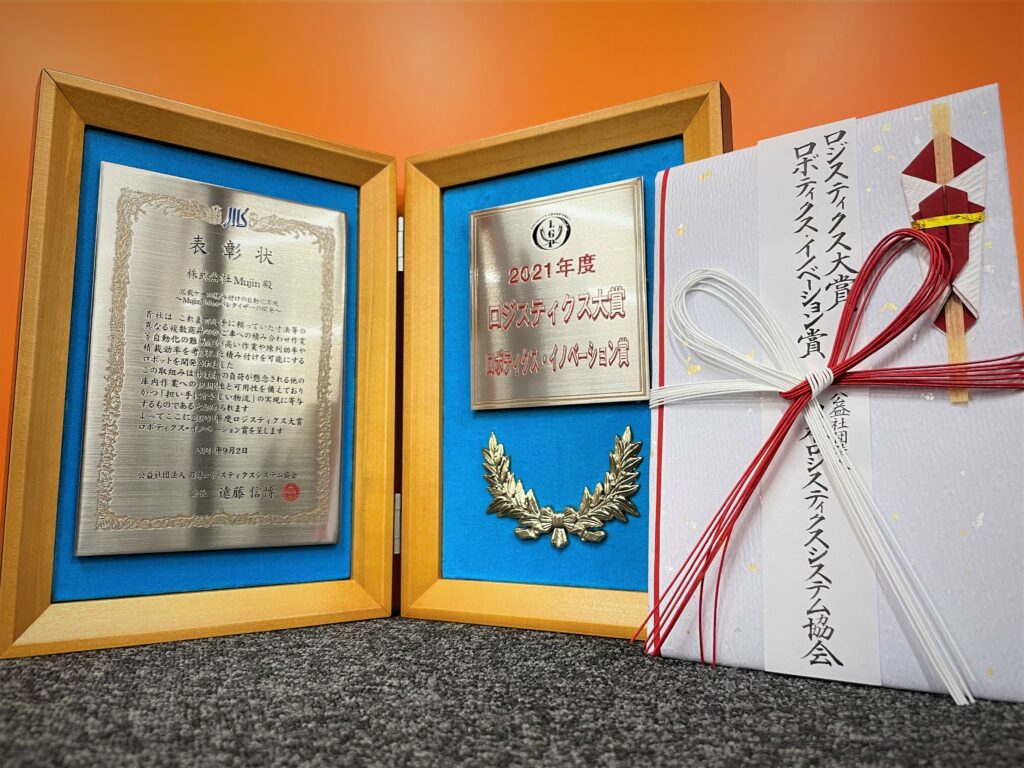
We would like to continue to promote the realization of an environment where people can work comfortably through the provision of MujinRobot.