E-commerce has exploded in past years. Today, you can have nearly any item imaginable arrive on your doorstep within 24-48 hours. As a result, we, consumers, have grown to expect that same level of service everywhere, demanding convenience, variety, and most importantly, speed. Retailers struggle to keep up with an ever-increasing volume of orders and escalating delivery demands. Order picking is one of the most important functions in e-commerce industries.
This article is about another Mujin’s logistics solution; read more about palletizing and depalletizing here: Robot Solutions For Logistics Automation: Depalletizing & Palletizing.
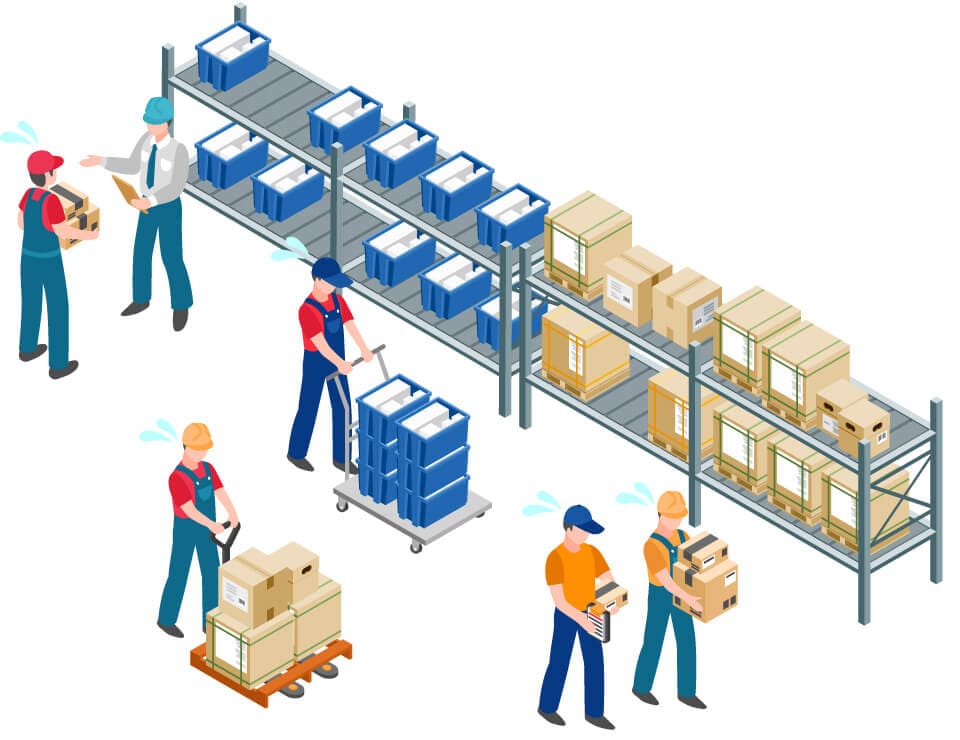
The problem comes down to pieces and people. By surging online order volume due to the shift to single-item shipping with double-digit growth spanning millions of SKUs, that is what we call the “pieces” problem. The “people” side of the problem comes from narrow labor markets in many regions, shrinking talent pools, and a tendency for people to avoid performing day-to-day routine task-based roles. The proportion of picking work at logistics centers is said to be about 60 to 70%. It is difficult to recruit for the kind of simple tasks where workers have to walk around picking out specific products. In recent years, as demand has increased, this has become a hindrance.
Automation of warehouse tasks using robotic piece-picking, designed to meet the new realities of e-commerce and to integrate with a wide range of warehouse systems is needed. Starting in 2015, with the business collaboration with ASKUL, a large mail order service company (Mujin Story #4: The opportunity to move from manufacturing to logistics), Mujin has been developing a piece-picking system to solve one of the most challenging problems in warehouse automation.
Mujin offering a wide range of robot automation applications for piece-shipping centers such as mail order and EC industries, extending from vehicle/container unloading in upstream warehouse logistics to midstream piece-picking and downstream palletizing. The technology can pick and place a wide range of items and fulfill orders at high speeds while ensuring that customers consistently receive what they ordered. The Mujin Controller is the world’s first all-purpose intelligent robot control system that involves real-time perception, motion planning, and control.
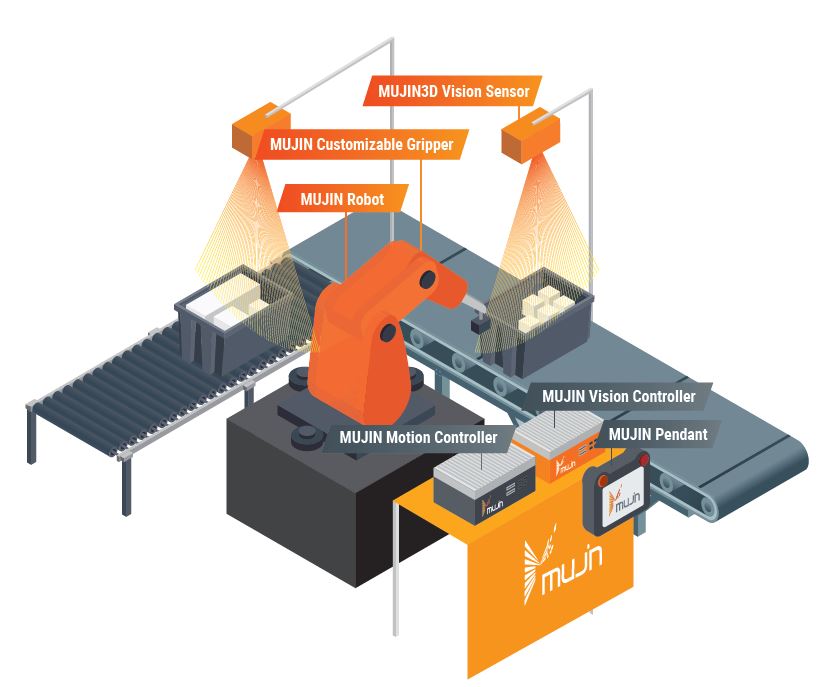
Piece-picking automation is one of the most challenging tasks.
Why?
Challenge #1: Handle range of items
Think about the items you can order online: a jar of jam, a box of bottled water, and a bag of rice. You, a human, could pick all of those items pretty easily by using your hands regardless of the size, the weight, and the shape of the item.
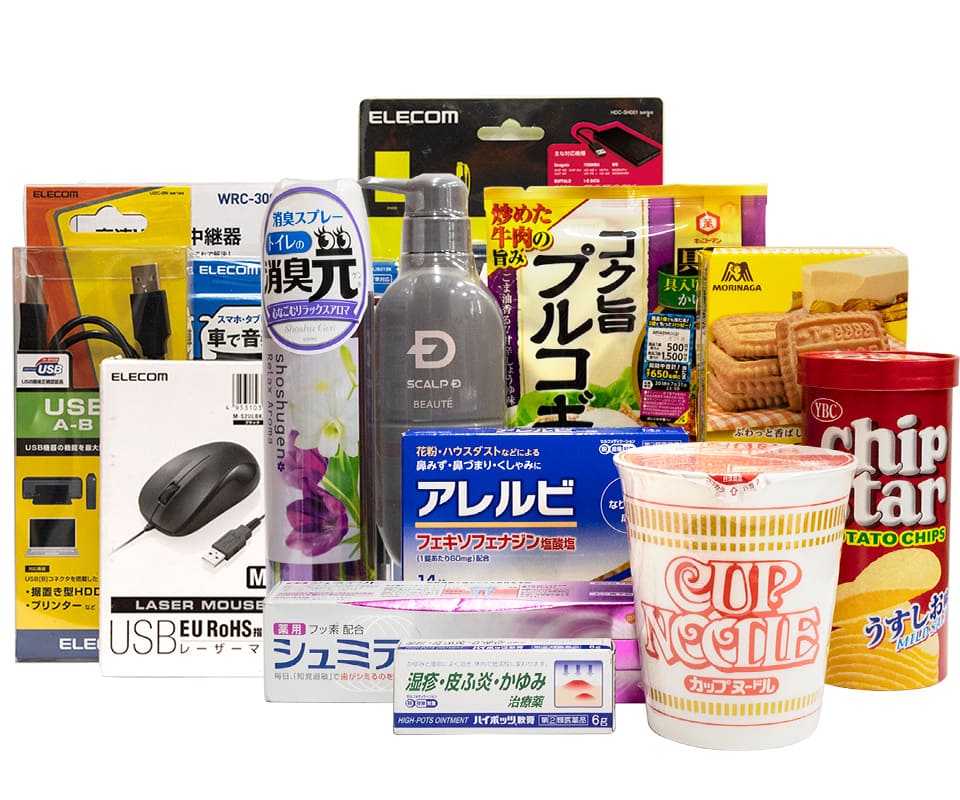
But for a robotic arm, it’s a different story. The box of bottled water is a heavy rectangular, while the jar is a cylinder, and the rice is in a flexible sack. Developing an arm with a vision system and a gripper that could properly identify and pick up each of those items (and thousands of others) correctly every time would be prohibitively expensive to build, to buy, to setup, and to maintain. The robot arm should be mechanically reliable, requiring little or no change to existing infrastructure when the new item comes. Two products may be accidentally taken because product-specific suction control cannot be performed. Heavy items may be thrown clear because the speed cannot be adjusted according to the product.
With no registration system just for box-type objects, vision recognition settings are required for each product type. There are many identically packaged tubes of toothpaste, bottles of shampoo, T-shirts, or various snack boxes for example. Design pattern registration is also impossible, so recognition mistakes occur. More SKUs the warehouse stocks, the greater the variety of these items, and the greater the size options offered.
Mujin’s proprietary 3D perception system is one of the most widely used picking perception systems. All kinds of objects, including feature-less objects, can be handled by Mujin, various items can be registered, from boxes to bottles. With Mujin’s proprietary registration system, anyone can easily register product types. Speeds and suction areas can be customized for each registered product to achieve more stable picking. With no prior robotics knowledge required, an average warehouse operator can let the robot recognize and pick a new SKU in a few minutes. More than 300,000 different types of objects have been recognized by Mujin’s system so far.
Robots power by Mujin can also provide and contribute to order integrity by validating an item, such as via barcode scan using Mujin Six-face in-the-air barcode scanning which provides an automatic scanning according to the barcode location, verifying that the proper inventory was presented to the piece-picking system.
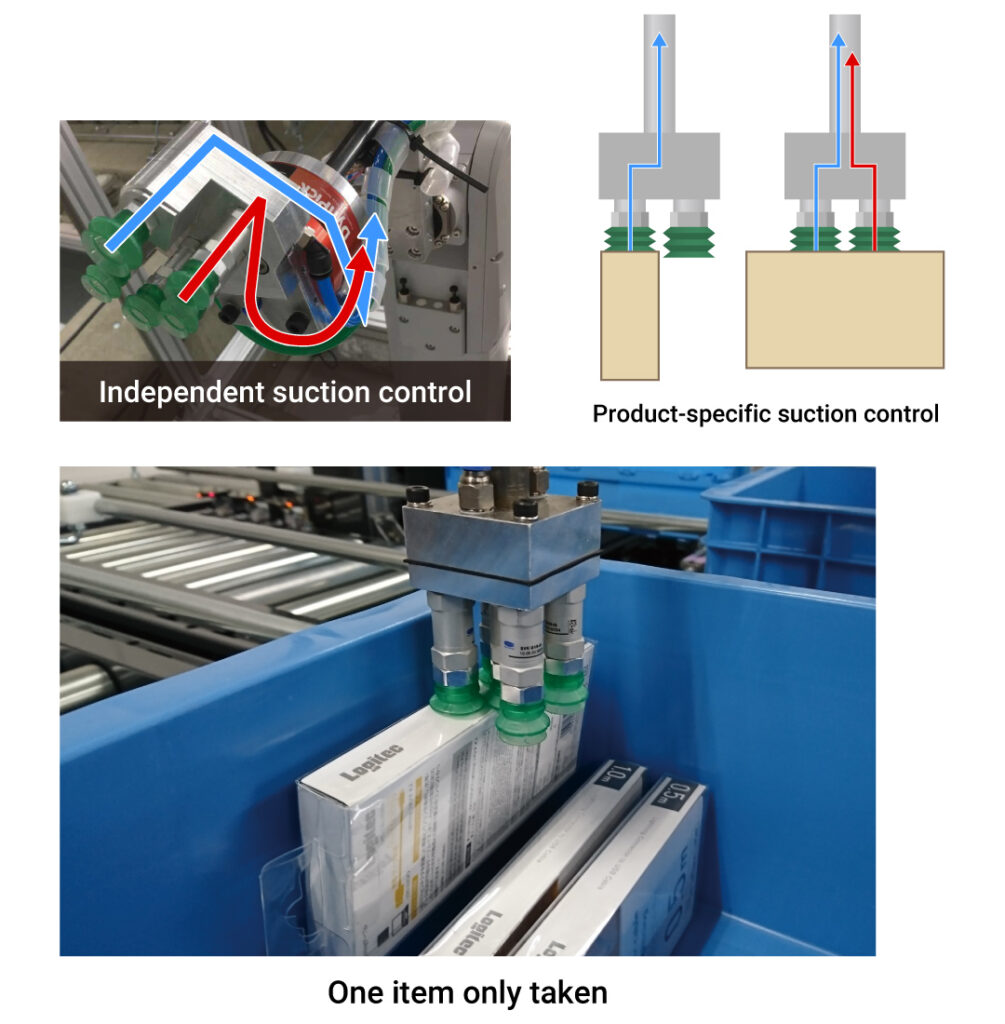
With Mujin solution handling many products is possible with a single hand or, if necessary, automatic hands switching. If the tool has to be changed, the user could expand the number of supported container sizes and varieties of target pieces. Product-specific suction control is performed so that two products will not be taken in error. The speed can be adjusted according to the product so, for example, speed is suppressed for heavier products, and a fine level of control can be performed.
Challenge #2: Pick the right item from disordered loads
Robotic piece-picking is reliable if it provides order integrity – always picking the right quantity, and successfully transferring it to the place location. Picking from a disordered loading condition is extremely difficult, as it requires extensive teaching for each type of product. Since neat packing cannot be performed well, space efficiency is poor. Ultimately, it is necessary to produce a flat loading state, which requires extra man-hours. Even if the warehouse has an automated conveyor and sorting systems, people play a key role in handling items as they move through the facility. A passageway is necessary for each row of shelving.
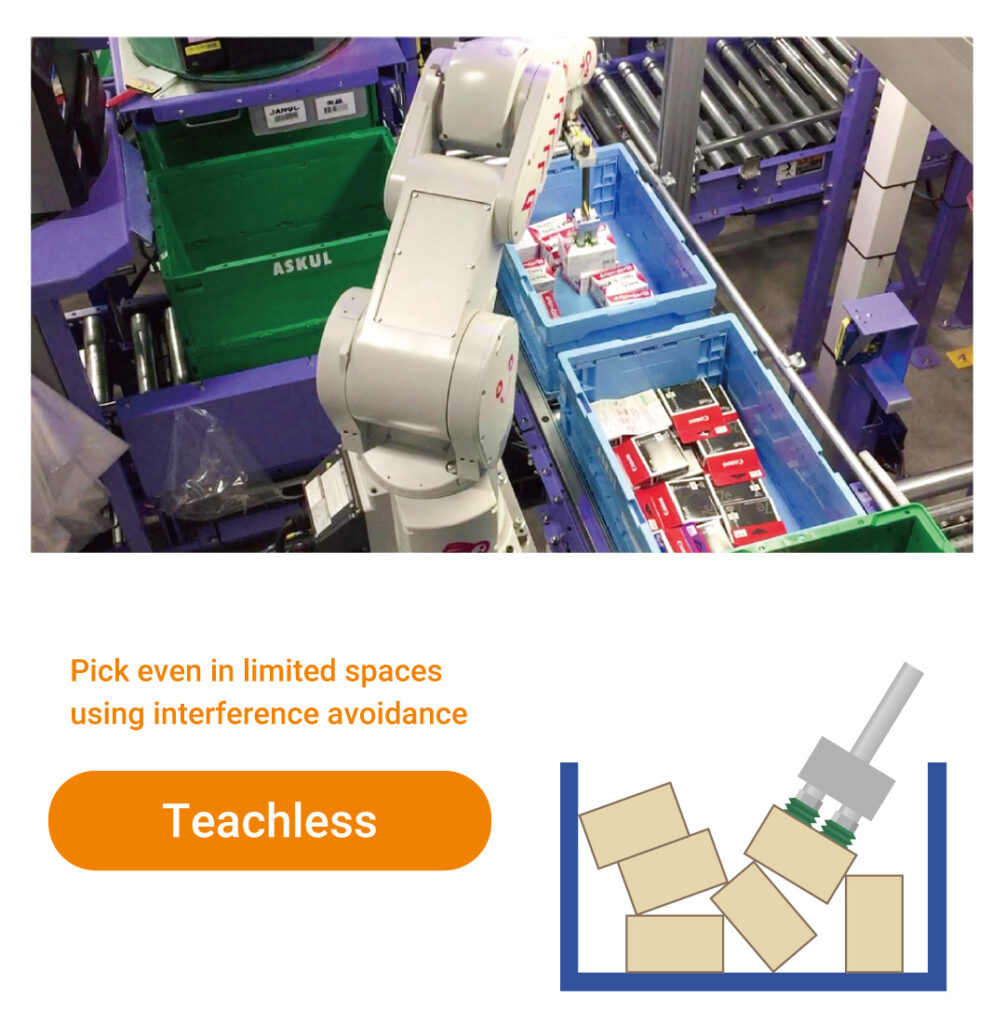
The Mujin Controller “Pick Worker” system can make any robot intelligent regardless of robot brand, it has necessary functions for piece-picking supplied all-in-one. With Mujin’s Teachless technology, picking can be automatically started whatever the loading condition and product are; it’s possible to start picking up robots in a few days. With the advanced interference avoidance function, deep boxes can be used as well. Because it is “Teachless”, a very large variety of products can be handled. The efficient packing allows to maximize container storage and minimize shipping cost.
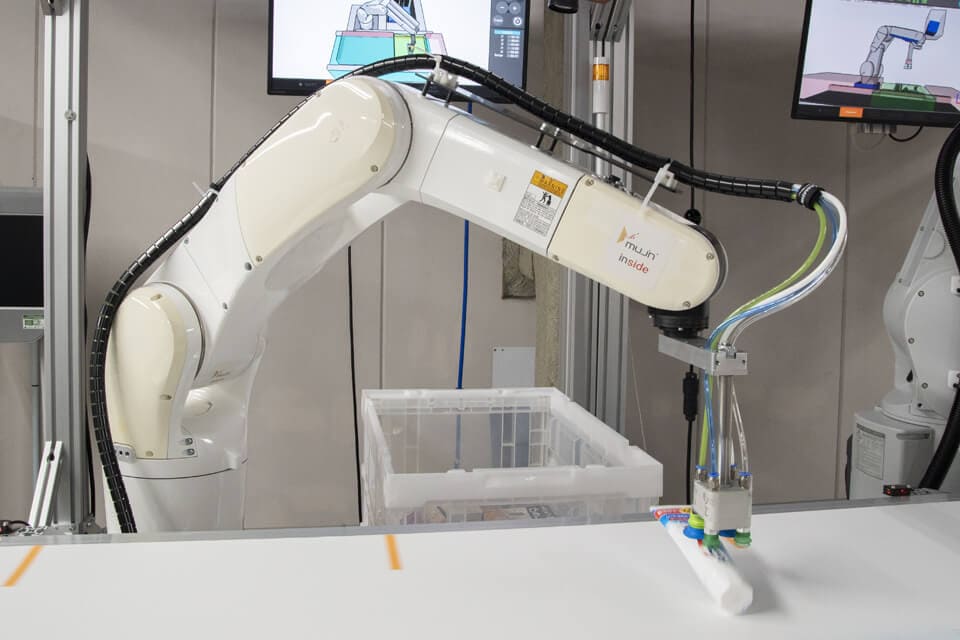
Batch-picked products can be inserted into the sorter or placed inside the box automatically without humans to be presented. With full automation, stable operation can be realized by maximizing the efficiency of the robots, picking mistakes and shipping mistakes are reduced. Space savings are achieved and high-level free secure and safe space (with no entry for humans) can be utilized to the maximum. “No resting. No stopping. No quitting.” is realized.
Challenge #3: Place neatly
The robot needs to pick and place successfully every time, without damaging products. With a teaching-based robot, it is not possible for the robot to be controlled in real-time so that it can adapt to the continually changing conditions within a box. Products can only be dropped from a fixed point over the box, which can damage them. Since neat packing cannot be performed well, space efficiency is poor.
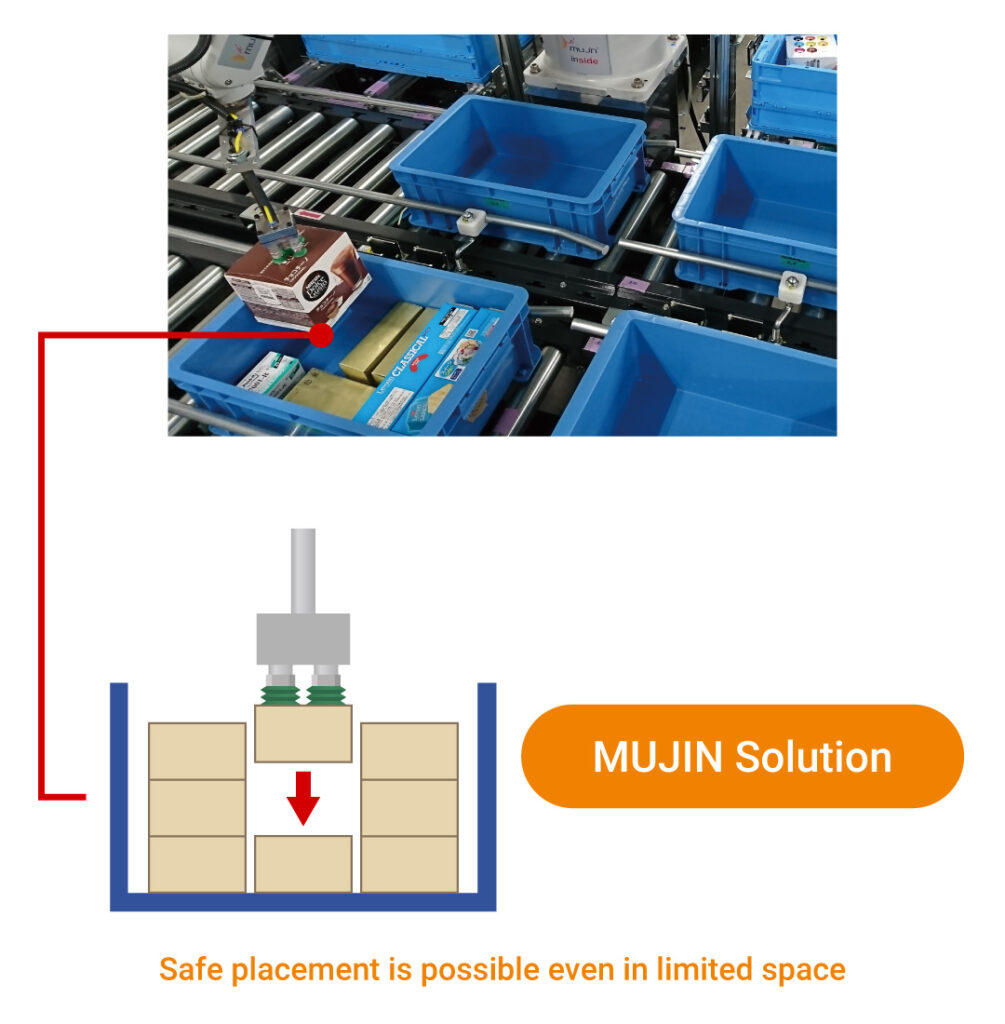
Mujin’s sensitive autonomous placement function won’t damage customers’ products. Products can be placed in the container with no gaps. Since products are placed aligned into gaps, as they would be by a human being, they are not damaged through collisions. Since the container on the placement side is also constantly monitored, when loads collapse, approaches will be made only after checking the situation. The gentle placing to avoid damage is suitable for high-valued products (e.g. electronics) or for zero-damage-tolerant products (e.g. pharmaceuticals).
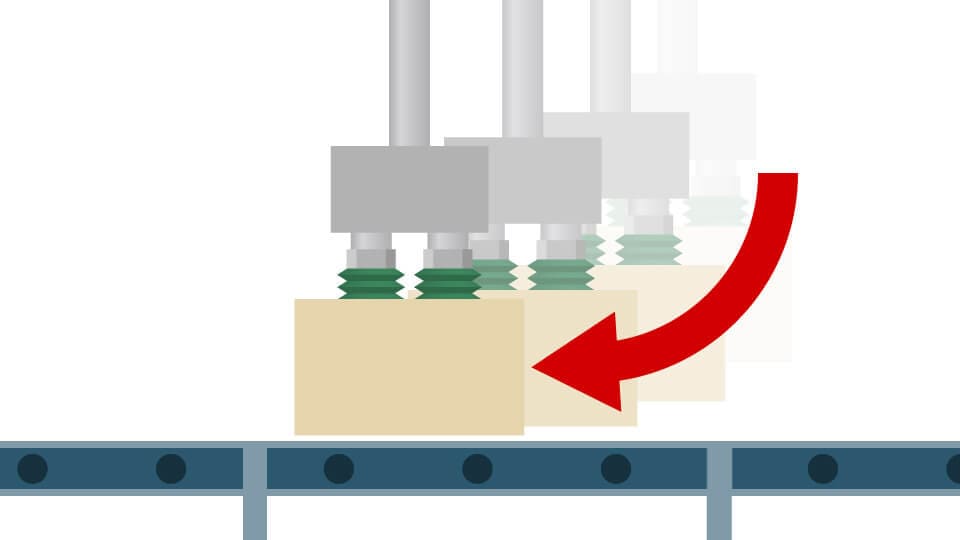
The control conveyor speed is important for insertion into a sorter, or DAS (digital assortment system). With Mujin, robotic automation extends from fixed point batch picking of products to subsequent insertion into the sorter. If the conveyor speed is high, the product may topple or, at worst, fall off. With Mujin, as with humans, it is possible to perform placement according to the speed of the conveyor. Light and sensitive control can be used to suppress falls and damage to products.
Successful stories
Mujin has not just overcome these challenges but also achieve the highest speed, Mujin piece-picking robot is the world’s fastest with a high picking capacity of 1000 pc/hour. In the latest next-generation warehouse, which started operation in 2020, Mujin’s fully automated piece-picking robot stations were deployed, which are now showing this speed results. Mujin achieved the highest level of quality (thorough quality control), safety (traceability), and efficiency (establishment of an efficient logistics environment) by introducing our cutting-edge technologies. This latest distribution center has introduced robots for picking (piece-picking rate is 95%), resulting in higher efficiency with less workload. Our customers are expecting more than 99.99999% shipment accuracy. Moreover, the guaranteed shipping accuracy allows omitting inspections at delivery to our customer’s clients. This enables to greatly reduce the inspection time for clients (No Inspection System).
Another Mujin customer, consumer electronics maker, has been working hard to automate operations in its logistics centers. Due to technical difficulties, the sorting process was never automated. Mujin took up the challenge and made it possible to achieve fully automated robot piece-picking from mixed-SKU containers, with gentle placing on fast-moving conveyors.
Apparel picking automation is challenging because of the nature and variety of items. Mujin partnered with Fast Retailing to help them improve efficiency in warehousing and distribution. Mujin developed the Intelligent Piece Picking Robot, which detects items with 3D vision and places items neatly in shipping boxes without damage. Also, the Mujin system can prevent mis-shipping by automatic inspection using 3D cameras to scan and log the contents of each package.